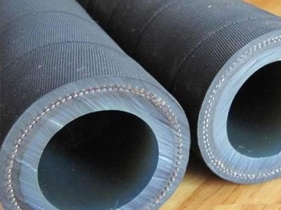
1. The use of protection cannot be ignored: the long-term use of high-pressure sand blasting hose joints at home usually does not cause concern, but excessive use and improper protection also buried the hidden danger of joint cracking to a certain extent. It is understood that the service life of the joint is usually 200000 times, and it should be replaced after long-term use. When using the side, Corbel tube Price Care should be taken to close and open as gently as possible and not to rotate the knob of the hose connector repeatedly. 2. Differentiation of quality can be based on standard evidence collection. It is understood that it is still difficult to determine the cause of joint cracking. At present, the National Bureau of Technology and Quality Supervision has issued recommendations for sealing nozzles and hose specifications. These two specifications perfectly adjust the quality specification target of connectors and hoses. Consumers can go to the quality inspection department to check the torsional strength of the connecting hose, the tightness of the connecting spool and the strength of the connecting materials. If the content of standard rules cannot be met, it will be attributed to quality problems, which can serve as a strong basis for expression. 3. The appearance of hose connector is difficult to distinguish between good and bad. In order to pursue profits and reduce costs, many manufacturers currently use selected cast iron (easy to rust) and zinc alloy (non anti-corrosion) as materials to produce high-pressure sand blasting hose joints, which causes product quality problems. It is understood that the quality of connectors and hoses is not up to standard, Huanggang Corbel tube The strength function and sealing function of high-pressure sand blasting hose joints are not up to standard due to problems such as materials and wall thickness, which should be paid attention to by consumers.
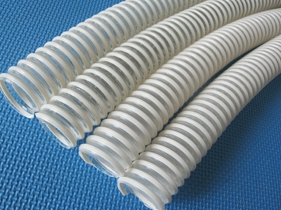
The hard core method adopts the core extrusion process to extrude the inner rubber tube blank, which directly uses the extruder to cover the inner rubber tube blank on the iron core, instead of the traditional casing process, and simplifies the process flow. Huanggang Corbel tube The billet forming adopts the process method of intertwining outer film and steel wire braiding forming. Similar to wrapping water wrapped cloth, the overlapping width is 1/2 of the film width. This process method can replace the method of wrapping outer film by extruder or by hand, reducing energy consumption and cost. We all know that the reinforcing layer and reinforcing layer of the rubber hose are the main force bearing parts, which are used to bear the load pressure. The factors determining the stress condition of the reinforced layer of the rubber hose are determined by the tension of the braided steel wire and the braiding angle. The high-speed steel wire hose braiding machine developed by our factory has introduced the advanced technology of foreign braiding production lines, and integrated the characteristics of domestic braiding machines. It integrates the advanced functions of hydraulic brake hose braiding production line, such as horizontal mechanical transmission, automatic lubrication, and so on, to develop equipment with high productivity and high degree of automation. The range of braiding diameter can be achieved Ф 6— Ф 25 Long core rubber hose (reinforcement layer). It fills the gap of domestic knitting production equipment, which can be widely used in rubber and plastic hose, rubber hose (reinforcement layer) knitting production equipment. The structure of high-pressure rubber hose is composed of four parts: inner liner, inner rubber layer, skeleton layer, middle rubber layer and outer rubber layer. Corbel tube Price In case of direct contact with the conveying medium, the synthetic rubber with good medium resistance, high tensile strength, high constant tensile stress, small compression permanent deformation and easy processing is usually selected. In order to meet the use requirements of strong polar medium resistance, the inner liner is composed of polytetrafluoroethylene layer and rubber layer, and a layer of film or adhesive is added on the surface of the inner liner to improve the adhesion with the skeleton material.
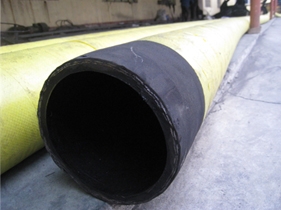
Huanggang Corbel tube Also called rubber hose for sand blasting. It is suitable for air pressure sand blasting of metal surface for rust removal, hemp removal, and sand blasting rubber hose for wet sand blasting and dry sand blasting in engineering construction. It is suitable for air pressure sand blasting of metal surface for rust removal, hemp removal, and sand blasting rubber hose for wet sand blasting and dry sand blasting in engineering construction. The common application fields are shipbuilding, machining, spraying industry, etc. Appearance of abrasion resistant sand blasting rubber hose: 1. Light abrasion resistant sand blasting rubber hose consists of black, yellowish or transparent abrasion resistant rubber inner layer, central fabric or cord reinforcement layer, medium rubber layer and outer rubber layer; 2. Heavy abrasion resistant rubber hose consists of black, yellowish or transparent abrasion resistant rubber inner layer, cloth clip or cord reinforcement layer, steel wire framework reinforcement layer, medium rubber layer Composition of outer rubber layer 3. The steel wire braided wear-resistant sandblasting hose is composed of black, yellowish or transparent wear-resistant rubber inner layer, single-layer or multi-layer steel wire braided reinforcement layer, medium rubber layer and outer rubber layer. Purpose Abrasion resistant sand blasting hose is a kind of material conveying pipe, which is mainly used for conveying solids containing particles such as particles, gravel, cement, quicksand, mud, gypsum, etc. It is suitable for various tunnel projects, tunnels, caverns and other engineering operations. The general working pressure is less than 12 bar, and the higher bursting pressure can reach 36 bar. Sometimes the vacuum rich negative pressure parameter is 0.8 bar 0.9 bar. Corbel tube Price Hydraulic requirements 1. The maximum working pressure of wear-resistant sand blasting hose is 0.63MPa. 2. The hose shall be free from water seepage, local bulge, expansion and other abnormalities when conducting hydraulic test under twice the working pressure. Keep the pressure of anti-static hose for 1min, and the length change shall not exceed ± 0.8%, the outer diameter change shall not exceed ± 10%, and the torsion per meter shall not exceed 60 º. 3. The bursting pressure of the hose shall not be less than 4 times of the working pressure.
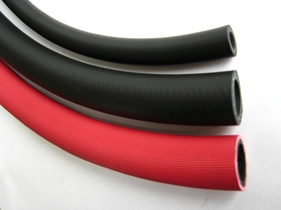
production Corbel tube It is a key component of any hydraulic system. When they fail, everything will stop. The preventive maintenance of the metal sandblasting hose is very important and needs to be checked regularly in order to find problems before starting. This may include checking hose caps and fittings, and looking for other signs of leaks and impending hose failure. The more strict the hose inspection process, the more reliable your equipment will be. 1. Benefits of preventive maintenance of metal sandblasting hoses: preventive maintenance of metal sandblasting hoses and equipment is always better than reactive maintenance. One reason is that it can make your equipment run efficiently by solving problems before they fail and have a significant negative impact on the system. Contrary to what many people think, preventive maintenance means reducing downtime due to unexpected component and system failures. Attention to maintenance can also extend the expected life of equipment, maximize its economic value, and minimize potential safety hazards to personnel. Finally, preventive maintenance can reduce maintenance costs and unnecessary equipment procurement. Not participating in regular preventive maintenance can be an expensive decision. 2. Maintenance time of metal sandblasting hose: Corbel tube Price Part of the preventive maintenance program for solid metal sandblasting hoses includes periodic inspection of metal sandblasting hoses. Fixed equipment shall be inspected every three months. For mobile equipment, hose inspection shall be conducted every three months or every 400 to 600 hours, whichever comes first.