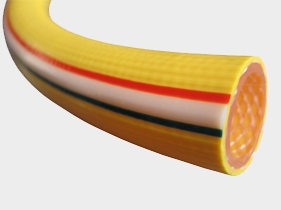
1. The use of protection cannot be ignored: the long-term use of high-pressure sand blasting hose joints at home usually does not cause concern, but excessive use and improper protection also buried the hidden danger of joint cracking to a certain extent. It is understood that the service life of the joint is usually 200000 times, and it should be replaced after long-term use. When using the side, Cord hose company Care should be taken to close and open as gently as possible and not to rotate the knob of the hose connector repeatedly. 2. Differentiation of quality can be based on standard evidence collection. It is understood that it is still difficult to determine the cause of joint cracking. At present, the National Bureau of Technology and Quality Supervision has issued recommendations for sealing nozzles and hose specifications. These two specifications perfectly adjust the quality specification target of connectors and hoses. Consumers can go to the quality inspection department to check the torsional strength of the connecting hose, the tightness of the connecting spool and the strength of the connecting materials. If the content of standard rules cannot be met, it will be attributed to quality problems, which can serve as a strong basis for expression. 3. The appearance of hose connector is difficult to distinguish between good and bad. In order to pursue profits and reduce costs, many manufacturers currently use selected cast iron (easy to rust) and zinc alloy (non anti-corrosion) as materials to produce high-pressure sand blasting hose joints, which causes product quality problems. It is understood that the quality of connectors and hoses is not up to standard, Hangzhou Cord hose The strength function and sealing function of high-pressure sand blasting hose joints are not up to standard due to problems such as materials and wall thickness, which should be paid attention to by consumers.
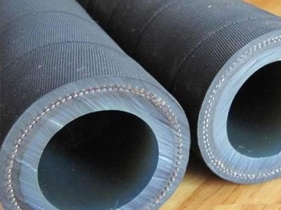
Hangzhou Cord hose The structure is composed of liquid resistant synthetic rubber inner rubber layer, medium rubber layer, I or II or III steel wire braid reinforcement layer, and weather resistant synthetic rubber outer rubber layer. Sand pumping hose features: 1. Sand pumping hose is made of special synthetic rubber, which has excellent oil resistance, heat resistance and aging resistance. 2. The rubber hose has high bearing pressure and excellent pulse performance. 3. The pipe body is tightly combined, soft to use, and has little deformation under pressure. 4. Sand pumping hose has excellent bending resistance and fatigue resistance. 5. The sand pumping hose is long, φ 20 meters above 32, φ Below 25 meters, it can reach 10 meters or even 100 meters. Sand pumping hose parameters: 1. The inner wall of nylon cord hose is smooth with little friction. Reinforcing layer: high-strength synthetic wire, spiral winding of steel wire and iron wire (sand suction pipe) 2 production Cord hose Flange connection (ANSI150 standard flange) 3. Nominal pressure: 20BAR4, temperature: - 50 ℃ -+95 ℃ 5. Working pressure of sand suction hose and mud discharge pipe: positive pressure: 10kg; Test pressure: working negative pressure of 15kg steel ring sand suction hose: ≥ 15kg sand suction hose has strong flexibility, which is mainly used as the sand pump sand discharge pipe to connect the sand transport pipe and sand pump, as well as the pipe connection bend.
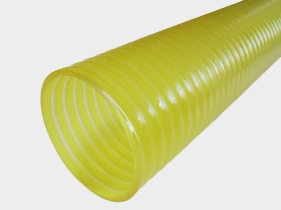
production Cord hose Acid and alkali resistance: there is no obvious change after soaking in 44 solutions for 24 hours; Pressure resistance: under the pressure of 52.5 MPa, the pressure is stable for 5 minutes without leakage, the surface of the pipe body is not deformed, and the damage pressure is greater than 105 MPa; Heat preservation: place the pipe in an environment of 300-50 ℃, with clear water in the pipe for 20 minutes, and the temperature ratio inside and outside the pipe is 1:40. The wear-resistant sand blasting hose is a material conveying pipe. The wear-resistant sand blasting hose is a material conveying pipe. Common black, yellowish or transparent; Most of them are wrapped by external rubber packing belt, and the steel wire is usually set between the internal and external rubber for negative pressure operation. The utility model is mainly used for conveying liquid containing solid particles such as particles, gravel, cement, quicksand, concrete, gypsum, etc., and is suitable for various tunnel projects, shafts, tunnels, and other engineering operations. The inner rubber and outer rubber of sand blasting pipe made of ordinary materials are usually made of wear-resistant materials, most of which are nitrile rubber (acrylonitrile butadiene copolymer), styrene butadiene rubber (oil extended styrene butadiene rubber), etc., Or PARA rubber (trefoil rubber), the inlet hose has better performance. According to the working conditions and the degree of loss of material particles to the transmission medium, the sand blasting pipe is generally divided into light sand blasting pipe and heavy sand blasting pipe. Spiral wire will make them suitable for negative pressure environment. Light sandblasting pipe Light sandblasting pipe Light sandblasting pipe is usually used in marine sandblasting and quicksand operations. The ordinary inner rubber is made of wear-resistant nitrile rubber (NBR), while the outer rubber is wrapped with composite rubber. Heavy sandblasting pipe Heavy sandblasting pipe Heavy sandblasting pipe is used for sandblasting sand, pebble, mud, etc. Equipment. Cord hose company Sand blasting vacuum tube Sand blasting vacuum tube The sand blasting vacuum tube is embedded with spiral steel wire, and the general vacuum negative pressure can reach 0.9 bar. Common parameter definitions The wear-resistant sandblasting pipe generally has the following parameters: folding pressure is generally within 12 bar, higher sandblasting pressure can reach 36 bar, and sometimes vacuum negative pressure parameters such as 0.8 bar~0.9 bar are required.
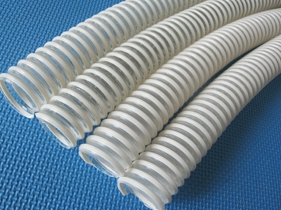
production Cord hose The inner rubber layer of( ф 0.3-2.0 reinforcement layer) is the skeleton material that plays the role of reinforcement. What should be paid attention to when storing the wear-resistant sandblasting pipe. 1. The wear-resistant sandblasting pipe should be stored as loose as possible. Generally, rubber hoses with inner diameter less than 76 mm can be wound and stored. 2. During the storage of wear-resistant sand blasting pipe, it is strictly prohibited to stack heavy objects on the pipe body to prevent external extrusion and damage. 3. During the storage of wear-resistant sand blasting pipe, do not contact with acid, alkali, oil, organic solvent or other corrosive liquids and gases, and the heat release should start from 1m away. 4. The storage period of wear-resistant sand blasting pipe shall not exceed 2 years, and it shall be used by the first person to prevent the quality of rubber pipe from being affected by long-term storage. 5. When wear-resistant sand blasting pipes need to be temporarily stored in the open air, the site should be flat and the rubber pipe should be laid flat. The upper cover should be placed under the rubber pipe and no heavy objects should be stacked. At the same time, the hose shall not contact the heat source. 6. The storage place of the upper and lower rubber pipes in the well shall be kept clean and ventilated, and the relative humidity shall be 80. The temperature of the storage place shall be kept between - 15 ℃ and 40 ℃, and the rubber pipe shall be protected from direct sunlight and water spray. 7. When storing wear-resistant sand blasting pipe, Cord hose company Both ends of the hose shall be sealed firmly to prevent sundries from entering the hose. 8. When the wear-resistant sand blasting pipe is stored, it should be placed separately according to different varieties and specifications, not mixed, and hang the management board. 9. In order to prevent the pipes from being pressed and deformed during storage, they should not be stacked too high, and the stacking height should not exceed 1.5m. It also requires rubber hoses to be "stacked" frequently during storage, at least once a quarter.
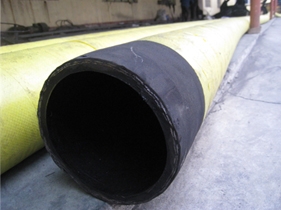
Cord hose company It has become the standard configuration of the modern new ball mill, but many problems may occur during the use or installation of the rubber lining plate, which will cause the failure of the rubber lining plate of the ball mill. Here is a brief introduction to the causes of the more common failure of the rubber lining plate of the ball mill. The design and installation are not professional and reasonable. The design and installation are also common problems for many novice manufacturers. For example, the bolt holes for fixing the ball mill lining plate are square, which will cause stress concentration and fracture. Adjust the size of lining plate to control the gap between lining plates at about 8mm; The installation quality of lining plate is very important to the safe operation of ball mill. First, tighten the fixed wedge symmetrically, put the lining plate in sequence, and then use the tightening wedge to secure it; Therefore, professional installation guidance can easily avoid these problems. The reason why the rubber lining plate of the ball mill does not match the steel ball is relatively common, and it is easy for many novice manufacturers to ignore and make mistakes. During the operation of the ball mill, the rubber lining plate of the ball mill, materials and steel balls promote the normal grinding and crushing of the ball mill due to the interaction of forces. The hardness of materials is related to wear resistance, and the wear resistance increases with the increase of hardness, Hangzhou Cord hose It is a pair of friction pairs, and the increase of hardness of one side will cause the wear of the other side to increase. Therefore, the high wear-resistant rubber lining plate is matched with the high wear-resistant steel ball, and the low wear-resistant rubber lining plate is matched with the low wear-resistant steel ball, so as to ensure the normal wear of the rubber lining plate of the ball mill and extend the service life of the ball mill.