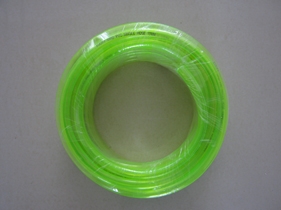
Handan Acid and alkali resistant rubber hose 1. The manufacturing quality shall be guaranteed according to the national standards of Oxygen Hose (GB/T2550-91) and Acetylene Hose (GB/T2551-91) respectively, and the hose shall have sufficient compressive strength and flame retardant characteristics. According to the national standard, the oxygen hose is red, the working pressure vessel is 1.5MPa, the inner diameter of the hose is 8mm, and the outer diameter is 18mm; 2. Care must be taken when storing and using the hose to keep it clean and free from damage. For example, avoid exposure to sunlight, rain and snow, and prevent contact with substances such as acid, alkali, oil and other organic solvents that can damage the hose. The storage temperature shall be - 15 ℃~40 ℃, and the distance from the personnel shall not be less than 1m; 3. When using a new hose, the talcum powder on the inner wall of the hose must be blown out first to prevent the channel of the welding torch from being blocked. Avoid external extrusion and mechanical damage during use, and do not fold the pipe body. 4. If the oxygen hose catches fire, stop the air supply first, and then deal with the fire hose, but do not bend the hose. The cylinder valve must be closed when the cylinder is not in use or after work. 5. The hose with bulge, crack or air leakage shall not be used, and the air leakage hose shall not be used after being stuck with adhesive tape. Acid and alkali resistant rubber hose company When connecting the two ends of the hose with tools, clamp or wire shall be used to fasten, and the intermediate joint shall be fastened with a gas pipe connector.
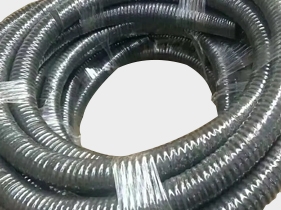
Acid and alkali resistant rubber hose company It has become the standard configuration of the modern new ball mill, but many problems may occur during the use or installation of the rubber lining plate, which will cause the failure of the rubber lining plate of the ball mill. Here is a brief introduction to the causes of the more common failure of the rubber lining plate of the ball mill. The design and installation are not professional and reasonable. The design and installation are also common problems for many novice manufacturers. For example, the bolt holes for fixing the ball mill lining plate are square, which will cause stress concentration and fracture. Adjust the size of lining plate to control the gap between lining plates at about 8mm; The installation quality of lining plate is very important to the safe operation of ball mill. First, tighten the fixed wedge symmetrically, put the lining plate in sequence, and then use the tightening wedge to secure it; Therefore, professional installation guidance can easily avoid these problems. The reason why the rubber lining plate of the ball mill does not match the steel ball is relatively common, and it is easy for many novice manufacturers to ignore and make mistakes. During the operation of the ball mill, the rubber lining plate of the ball mill, materials and steel balls promote the normal grinding and crushing of the ball mill due to the interaction of forces. The hardness of materials is related to wear resistance, and the wear resistance increases with the increase of hardness, Handan Acid and alkali resistant rubber hose It is a pair of friction pairs, and the increase of hardness of one side will cause the wear of the other side to increase. Therefore, the high wear-resistant rubber lining plate is matched with the high wear-resistant steel ball, and the low wear-resistant rubber lining plate is matched with the low wear-resistant steel ball, so as to ensure the normal wear of the rubber lining plate of the ball mill and extend the service life of the ball mill.
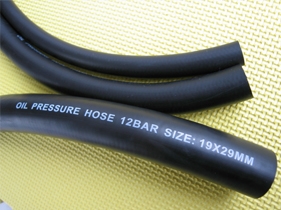
Handan Acid and alkali resistant rubber hose The structure is composed of liquid resistant synthetic rubber inner rubber layer, medium rubber layer, I or II or III steel wire braid reinforcement layer, and weather resistant synthetic rubber outer rubber layer. Sand pumping hose features: 1. Sand pumping hose is made of special synthetic rubber, which has excellent oil resistance, heat resistance and aging resistance. 2. The rubber hose has high bearing pressure and excellent pulse performance. 3. The pipe body is tightly combined, soft to use, and has little deformation under pressure. 4. Sand pumping hose has excellent bending resistance and fatigue resistance. 5. The sand pumping hose is long, φ 20 meters above 32, φ Below 25 meters, it can reach 10 meters or even 100 meters. Sand pumping hose parameters: 1. The inner wall of nylon cord hose is smooth with little friction. Reinforcing layer: high-strength synthetic wire, spiral winding of steel wire and iron wire (sand suction pipe) 2 production Acid and alkali resistant rubber hose Flange connection (ANSI150 standard flange) 3. Nominal pressure: 20BAR4, temperature: - 50 ℃ -+95 ℃ 5. Working pressure of sand suction hose and mud discharge pipe: positive pressure: 10kg; Test pressure: working negative pressure of 15kg steel ring sand suction hose: ≥ 15kg sand suction hose has strong flexibility, which is mainly used as the sand pump sand discharge pipe to connect the sand transport pipe and sand pump, as well as the pipe connection bend.
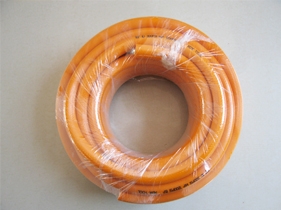
production Acid and alkali resistant rubber hose 1. During the molding of rubber products, the cohesive force of the elastomer cannot be eliminated due to the large pressure pressing. During the molding and mold release, extremely unstable shrinkage (the shrinkage rate of rubber varies due to different rubber types) often occurs. It must take a period of time before it can be gentle and stable. Therefore, at the beginning of the design of a rubber product, no matter the formula or the mold, it is necessary to carefully calculate the matching. If not, it is easy to cause dimensional instability of the product, resulting in low product quality. 2. Rubber belongs to thermosetting elastomer, while plastic belongs to thermosetting elastomer. Due to different sulfide types, the temperature range of rubber molding and curing is quite different, even affected by climate change and indoor temperature and humidity. Therefore, the production conditions of rubber products need to be properly adjusted at any time. If not, there may be differences in product quality. 3. The rubber product is the rubber mixture made from rubber raw materials after mixing in the internal mixer as the raw material. The formula is designed according to the characteristics of the required rubber products during mixing, and the required product hardness is determined. The product is molded by the rubber plate vulcanizer. After the product is formed, flash processing shall be carried out to make the product surface smooth without burrs. 4. The aging test of rubber products belongs to the category of aging test. Rubber aging refers to the phenomenon that the performance and structure of rubber and products are changed due to the combined effect of internal and external factors in the process of processing, storage and use, thus losing their use value. Acid and alkali resistant rubber hose company It is characterized by cracking, tackiness, hardening, softening, chalking, discoloration, mildew, etc. The following conditions shall be met when the ball mill uses the rubber lining plate: 1. The hardness of the ground material. The iron base alloy is similar to the rubber lining plate for materials below medium hardness, and the rubber lining plate is superior for materials above medium hardness. 2. The temperature of rubber lining plate is generally 70 ℃ - 90 ℃, and it can reach 110-130 ℃ under special circumstances. The temperature should be lower during dry grinding. 3. Feed size. Generally, the ball mill shall be more than 20-25mm; For the autogenous mill, the feeding particle size can be larger because no steel ball is added.
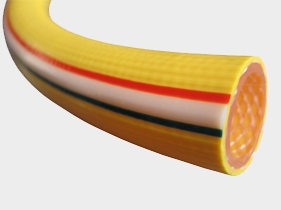
production Acid and alkali resistant rubber hose It will burst for a long time due to frequent and severe pressure shocks. This situation is usually not caused by excessive static pressure, but is related to the strength and frequency of pressure shock. During the operation of construction machinery, the oil pressure in the oil resistant hose will rise or fall repeatedly, and then it will form frequent pressure shocks to the oil pipe, causing the oil seal of each part to become more damaged, the oil resistant hose will bubble and break, and the pipe joint will become loose and leak. Therefore, in the process of operation, the valve rod should not be pulled too hard, and it needs to be gentle. The application temperature of the oil in the oil resistant rubber hose is too high, resulting in aging and bursting of the rubber hose. During the operation of construction machinery, the hydraulic system will cause the oil to become hot due to power failure, and the influence of external temperature (especially in summer) will cause the oil temperature to rise sharply. The higher the oiling temperature is, the easier the rubber hose ages, the worse the elasticity is, the lower the strength and sealing function are, and the oil resistant hose will burst quickly. Therefore, Acid and alkali resistant rubber hose company During operation, when the temperature rise of the hydraulic system is too high or too fast, the causes should be found and eliminated in time. Necessary cooling measures shall be taken for summer operation, especially continuous operation.
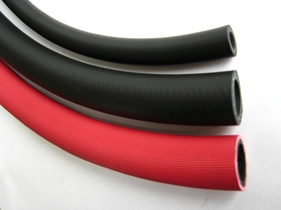
Prof. Weina, University of New South Wales, Australia? Sahajwara has developed a new method of using waste rubber and plastic for steel production - polymer injection process. Handan Acid and alkali resistant rubber hose It can not only greatly reduce the environmental pollution caused by waste rubber and waste plastics, but also effectively reduce the cost of steel production. Waste rubber and plastic contain a lot of carbon. Waste rubber and plastic are put into the electric arc furnace as substitutes for carbon element. The carbon originally locked in the waste plastic hose will react at ultra-high temperature and burn with coal to become clean fuel, thus reducing greenhouse gas emissions, At the same time, it also alleviates the environmental pollution caused by using them as landfill. The advantage of polymer injection process is that by injecting polymer and coke or anthracite rubber tube mixture, the volume of slag can be increased and the foaming degree can be increased, which can extend the arc length, increase the heat transfer from the arc to steel, reduce the heat loss through the slag and side walls, and thus improve the power efficiency. This reduces power consumption by about 3%. For every 1 ton of steel, about 24% of the cost comes from the cost of electricity. After polymer injection technology is adopted, each furnace of steel is, Acid and alkali resistant rubber hose company The average total amount of carbon injected can be reduced by 10%~20%. In addition, the potential price of polymer is lower than that of coke, and the total cost of carbon injection can be saved by 15%~35%.