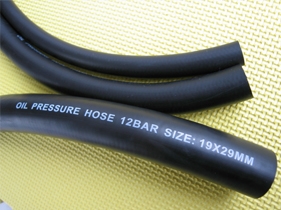
We all know rubber liner Where can I find it? The noise pollution in industrial production is very serious, and noise pollution is also an important factor affecting workers' enthusiasm for production. Ball mills were once a major source of noise in mining equipment. In order to reduce the noise generated by ball mills, protect the physical and mental health of workers, improve workers' enthusiasm for production, and create greater profits for the company, Through the efforts and research of domestic and foreign industry experts, the ball mill liner has been transformed. Through repeated tests and comparison, it is found that the noise generated by the rubber liner and the manganese steel liner of the ball mill is far less than the manganese steel liner when the technical parameters are up to standard. According to the data provided by the noise monitoring station and the concentrator, We analyzed the noise intensity and the economic benefits: the domestic ND2 precision sound level meter and octave filter were used for detection, and the sound level meter was calibrated by the provincial sound level meter measurement and verification station; There is no sound insulation room in the ball mill workshop. The monitoring points are arranged according to the position of the ball mill and the flow of workers to observe the mechanical operation, 2m away from the sound source. One monitoring point is respectively set on the left and right of the east and west of the workshop and in the middle of the two ball mills. The measurement method is in accordance with the Noise Detection Specification for Industrial Enterprises. As the noise in the workshop is continuous and steady, sound level A is used as the evaluation basis. The rubber lining plate is manufactured by Hainan Rubber Lining Plate Factory according to the ball mill shell structure and the original manganese steel lining plate specification (1.4mx0.74mX0.07m). Taiyuan rubber liner First, take out the manganese steel lining plate in the ball mill barrel, and then install the rubber lining plate in the barrel in turn (front and back). Each ball mill is installed with 48 pieces. First, use the pressure strip to compress, and then use the screws to fix the rubber lining plate on the ball mill barrel, so as to prevent falling off when rotating. The noise intensity of the ball mill workshop with manganese steel liner is 94-103dB (A), while the noise intensity of the ball mill workshop with rubber liner is 87-92dB (A), and the noise reduction difference is 7-11dB (A). The rubber liner has good noise reduction effect.
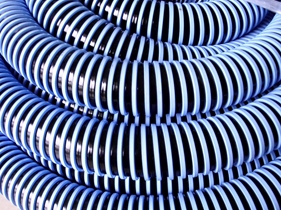
Taiyuan rubber liner 1. The manufacturing quality shall be guaranteed according to the national standards of Oxygen Hose (GB/T2550-91) and Acetylene Hose (GB/T2551-91) respectively, and the hose shall have sufficient compressive strength and flame retardant characteristics. According to the national standard, the oxygen hose is red, the working pressure vessel is 1.5MPa, the inner diameter of the hose is 8mm, and the outer diameter is 18mm; 2. Care must be taken when storing and using the hose to keep it clean and free from damage. For example, avoid exposure to sunlight, rain and snow, and prevent contact with substances such as acid, alkali, oil and other organic solvents that can damage the hose. The storage temperature shall be - 15 ℃~40 ℃, and the distance from the personnel shall not be less than 1m; 3. When using a new hose, the talcum powder on the inner wall of the hose must be blown out first to prevent the channel of the welding torch from being blocked. Avoid external extrusion and mechanical damage during use, and do not fold the pipe body. 4. If the oxygen hose catches fire, stop the air supply first, and then deal with the fire hose, but do not bend the hose. The cylinder valve must be closed when the cylinder is not in use or after work. 5. The hose with bulge, crack or air leakage shall not be used, and the air leakage hose shall not be used after being stuck with adhesive tape. rubber liner Where can I find it? When connecting the two ends of the hose with tools, clamp or wire shall be used to fasten, and the intermediate joint shall be fastened with a gas pipe connector.
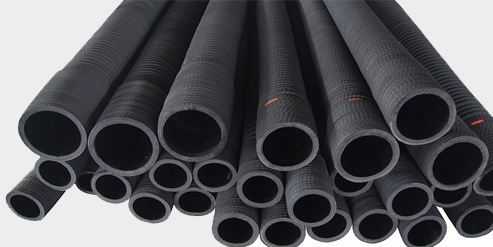
Due to the limitation of spatial location conditions, high quality rubber liner The installation stress of can often bring various difficulties to the installation work: formed pipes cannot be installed; When you bend down, you are about to come. If you make do with pipes, local cold correction will inevitably occur. According to the size of the pipeline and the specific situation on site, the cold correction amount varies from several millimeters to tens of millimeters, some as high as hundreds of millimeters. Practice has proved that the greater the quantity, the higher the internal stress. These residual installation stresses in the rubber sand blasting pipe are undoubtedly huge hidden information. The lubricating oil duct of a certain type of engine bearing was broken for many times due to excessive installation stress in actual operation. Because it can be bent at will, the internal stress generated by bending under the condition of rated bending radius is very small, which brings great convenience to the installation work, and also plays a certain role in ensuring the safe operation of the rubber sand blasting pipe. This is the main reason why some rubber sand blasting pipes must be used. Since it is necessary to load and unload the mold, the movable cylinder on the vulcanizer will move up and down. After repeated reciprocation, the copper serpentine tube will undergo fatigue fracture. Although it can continue to be used after repair, stopping for repair will cause time loss. Taiyuan rubber liner Although it has good flexibility and strong fatigue resistance, it is also weak in pressure bearing, temperature resistance, aging resistance and other aspects, and can not be used after several months. The good comprehensive performance of rubber sand blasting pipe is fully reflected here.
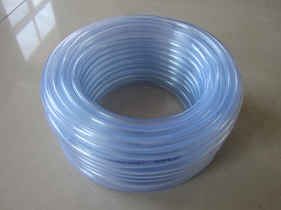
rubber liner Where can I find it? The following recommendations contain a series of precautions to prevent items from aging to a greater extent during storage. 1. During storage, the rotating plan system shall be adopted to shorten the storage time of high-pressure braided hose as much as possible. If long-term storage cannot be avoided and the following recommendations cannot be followed, high-pressure braided hoses should be thoroughly inspected before use. 2. Physical storage conditions: The high-pressure braided hose must be stored without mechanical pressure, including excessive stretching, compression or deformation, and without contact with sharp or sharp objects. High pressure braided hoses should be stored on suitable supports or on dry ground. High pressure braided rubber tubes packaged as coils must be stored horizontally. High pressure braided rubber pipes shall not be stacked. If stacking cannot be avoided, the stacking height shall not cause permanent deformation of the high-pressure braided rubber pipe below. Pumping high-pressure hydraulic hose is a common high-pressure hydraulic hose. In order to ensure the operation safety of the pumped high-pressure hydraulic hose, the following small series will briefly introduce the correct use of the pumped high-pressure hydraulic hose: 1. Before each use of the high-pressure hydraulic hose, the surface of the high-pressure hydraulic hose must be evenly coated with soap liquid, which can play a non bonding role between the high-pressure hydraulic hose and the concrete, and play a lubricating role in the drawing process, It can greatly increase the reuse times of high-pressure hydraulic hoses. 2. Installation: first, insert the steel hinge wire into the inner hole of the draw tube to avoid extrusion deformation when pouring concrete. Then, pull out the high-pressure hydraulic hose coated with soap liquid from the prestressed hole and fix it in the correct position with a fixing ring. The spacing of the retaining rings is controlled by the suspension and is usually about 500 mm. high quality rubber liner When connecting the high-pressure hydraulic hose, wrap both ends of the high-pressure hydraulic hose for one and a half weeks or two weeks with thin iron sheet or PVC pipe (vertical cutting), fix them with iron wire, and then seal both ends of the PVC pipe with tape to avoid entering the mortar.