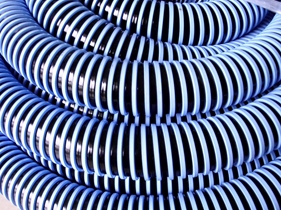
We all know Acid and alkali resistant rubber hose company The noise pollution in industrial production is very serious, and noise pollution is also an important factor affecting workers' enthusiasm for production. Ball mills were once a major source of noise in mining equipment. In order to reduce the noise generated by ball mills, protect the physical and mental health of workers, improve workers' enthusiasm for production, and create greater profits for the company, Through the efforts and research of domestic and foreign industry experts, the ball mill liner has been transformed. Through repeated tests and comparison, it is found that the noise generated by the rubber liner and the manganese steel liner of the ball mill is far less than the manganese steel liner when the technical parameters are up to standard. According to the data provided by the noise monitoring station and the concentrator, We analyzed the noise intensity and the economic benefits: the domestic ND2 precision sound level meter and octave filter were used for detection, and the sound level meter was calibrated by the provincial sound level meter measurement and verification station; There is no sound insulation room in the ball mill workshop. The monitoring points are arranged according to the position of the ball mill and the flow of workers to observe the mechanical operation, 2m away from the sound source. One monitoring point is respectively set on the left and right of the east and west of the workshop and in the middle of the two ball mills. The measurement method is in accordance with the Noise Detection Specification for Industrial Enterprises. As the noise in the workshop is continuous and steady, sound level A is used as the evaluation basis. The rubber lining plate is manufactured by Hainan Rubber Lining Plate Factory according to the ball mill shell structure and the original manganese steel lining plate specification (1.4mx0.74mX0.07m). Jinan Acid and alkali resistant rubber hose First, take out the manganese steel lining plate in the ball mill barrel, and then install the rubber lining plate in the barrel in turn (front and back). Each ball mill is installed with 48 pieces. First, use the pressure strip to compress, and then use the screws to fix the rubber lining plate on the ball mill barrel, so as to prevent falling off when rotating. The noise intensity of the ball mill workshop with manganese steel liner is 94-103dB (A), while the noise intensity of the ball mill workshop with rubber liner is 87-92dB (A), and the noise reduction difference is 7-11dB (A). The rubber liner has good noise reduction effect.
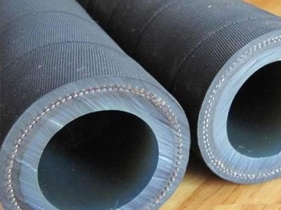
Jinan Acid and alkali resistant rubber hose The break of the sandblasting hose usually refers to the appearance and change of the crack of the sandblasting hose. The sandblasting hose has one or more cracks, but the cracks are neat. Another is that the internal bending cracks at the crack of the sandblasting hose are neat. The causes of different errors are different, and the treatment methods are also different. Therefore, in the process of using or protecting the sandblasting hose, the sandblasting hose should not be subject to changing torque. When installing the sandblasting hose, try to keep the axis of the two joints on the same plane to avoid twisting the sandblasting hose in use. Therefore, be careful with the application, and try not to make the sandblasting hose change excessively to avoid consumption. Sand blasting hose plays a very important role in the industry. Its inner rubber layer is added with carbon black, which can effectively eliminate static electricity and directly contact with compressed air and abrasives. The requirement for wear resistance is quite high. Once worn through, the reinforcement layer will be exposed, and the sand blasting hose will burst. The reinforcing layer of sandblasting hose is a pressure resistant layer, so high quality Acid and alkali resistant rubber hose The material and layout of the reinforcement layer directly determine the pressure rating of the sandblasting hose. There are two common enhancement layers: cloth clip enhancement layer and surround enhancement layer. The sand blasting hose with an inner diameter of 50mm or more is mostly used in the construction occasions where the sand blasting pipe needs to be extended to reduce the pressure loss in the sand blasting hose and ensure the normal operation of shot blasting.
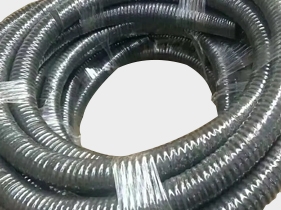
Jinan Acid and alkali resistant rubber hose It is a kind of hose that can be used for sand pumping and sand suction produced with high abrasion resistant rubber. It is often used in sand blasting industry, cement, steel, minerals and other industries, but it is mainly used in river dredging, slurry transportation in mines, sand digging and sand taking and other industries to transport sharp granular solids or solid-liquid mixtures. Its product structure is composed of high wear-resistant layer, reinforced water pipe layer, skeleton steel wire and outer rubber. Today, Myers will introduce the application field of wear-resistant sand absorption rubber pipe. When the wear-resistant sand suction rubber pipe is applied in the mine pit, it is necessary to set a floating boat equipped with a sand pump in the mine pit, and use the floating sand suction rubber pipe to connect with the sand pump. The floating boat will float up and down with the rise and fall of the water level. It is required that the pipe body has good flexibility and good tear resistance and bending resistance. The offshore pipeline is connected by non floating sand suction hose until the pulp transportation destination. The overall pipeline is divided into two parts, one for surface use and the other for onshore use. The main raw material of these two kinds of hoses is high abrasion and corrosion resistant rubber, and cord reinforcement layer and steel wire skeleton layer are added in the pipe wall to ensure the pressure resistance and tear resistance of the hose. The connection mode is vulcanized flange connection, that is, the flange and the hose are a whole, so there is no need to worry about the flange falling off. Floating sand suction hose used on the water surface. This kind of hose is required to float on the water surface. Due to the large drop of the mine (100 meters) and the long conveying distance Acid and alkali resistant rubber hose company The hose shall have high pressure resistance, and the design pressure is 25 kg/cm2 according to the calculation. It should be considered that the floating ship will move up and down with the rise and fall of the water level and the wave will cause lateral displacement. Its internal structure is the same as the sand suction hose used offshore, except that a floating body is installed outside the hose.
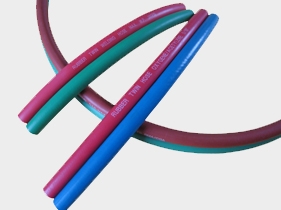
I believe everyone is familiar with high quality Acid and alkali resistant rubber hose Relevant application knowledge of products. It is understood that at present, this product is mainly used for mining hydraulic support and oilfield development. It is applicable to engineering construction, lifting transportation, metallurgical forging, mining equipment, ships, injection molding machinery, agricultural machinery, various machine tools, mechanization of various industrial departments, water-based liquids, etc. And liquid transmission. Its relatively high working pressure can reach 70-120 MPa. In order to achieve better application effect, what problems should be paid attention to when using high-pressure braided hose? 1. The bending radius shall not be less than the given bending radius to prevent damage to the hose skeleton or premature failure due to excessive tension. 2. Select the type and specification of the hose correctly according to the use conditions, and do not misuse or replace it. 3. When using high-pressure braided hose, the pressure should be adjusted slowly and evenly to avoid sudden pressure increase and damage to the pipe body. 4. When the work site changes, it should be removed from the ground without dragging, so as to avoid the skeleton layer being corroded after scratching the outer glue. 5. After delivering corrosive liquid, the interior should be cleaned to prevent residues from corroding the pipe body for a long time, or select corresponding series of products. When storing high-pressure braided rubber hoses, depending on the type of rubber used, Acid and alkali resistant rubber hose company Note which conditions typically change over time. However, due to several factors or a combination of several factors, this change may accelerate, and other materials used to strengthen high-pressure braided hoses may also be adversely affected by improper storage conditions.
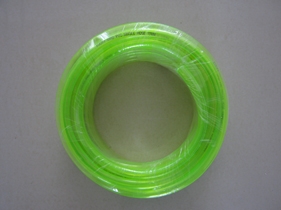
Due to the limitation of spatial location conditions, high quality Acid and alkali resistant rubber hose The installation stress of can often bring various difficulties to the installation work: formed pipes cannot be installed; When you bend down, you are about to come. If you make do with pipes, local cold correction will inevitably occur. According to the size of the pipeline and the specific situation on site, the cold correction amount varies from several millimeters to tens of millimeters, some as high as hundreds of millimeters. Practice has proved that the greater the quantity, the higher the internal stress. These residual installation stresses in the rubber sand blasting pipe are undoubtedly huge hidden information. The lubricating oil duct of a certain type of engine bearing was broken for many times due to excessive installation stress in actual operation. Because it can be bent at will, the internal stress generated by bending under the condition of rated bending radius is very small, which brings great convenience to the installation work, and also plays a certain role in ensuring the safe operation of the rubber sand blasting pipe. This is the main reason why some rubber sand blasting pipes must be used. Since it is necessary to load and unload the mold, the movable cylinder on the vulcanizer will move up and down. After repeated reciprocation, the copper serpentine tube will undergo fatigue fracture. Although it can continue to be used after repair, stopping for repair will cause time loss. Jinan Acid and alkali resistant rubber hose Although it has good flexibility and strong fatigue resistance, it is also weak in pressure bearing, temperature resistance, aging resistance and other aspects, and can not be used after several months. The good comprehensive performance of rubber sand blasting pipe is fully reflected here.
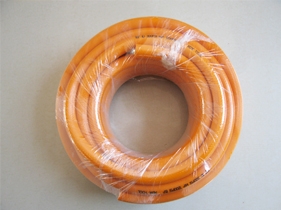
Prof. Weina, University of New South Wales, Australia? Sahajwara has developed a new method of using waste rubber and plastic for steel production - polymer injection process. Jinan Acid and alkali resistant rubber hose It can not only greatly reduce the environmental pollution caused by waste rubber and waste plastics, but also effectively reduce the cost of steel production. Waste rubber and plastic contain a lot of carbon. Waste rubber and plastic are put into the electric arc furnace as substitutes for carbon element. The carbon originally locked in the waste plastic hose will react at ultra-high temperature and burn with coal to become clean fuel, thus reducing greenhouse gas emissions, At the same time, it also alleviates the environmental pollution caused by using them as landfill. The advantage of polymer injection process is that by injecting polymer and coke or anthracite rubber tube mixture, the volume of slag can be increased and the foaming degree can be increased, which can extend the arc length, increase the heat transfer from the arc to steel, reduce the heat loss through the slag and side walls, and thus improve the power efficiency. This reduces power consumption by about 3%. For every 1 ton of steel, about 24% of the cost comes from the cost of electricity. After polymer injection technology is adopted, each furnace of steel is, Acid and alkali resistant rubber hose company The average total amount of carbon injected can be reduced by 10%~20%. In addition, the potential price of polymer is lower than that of coke, and the total cost of carbon injection can be saved by 15%~35%.