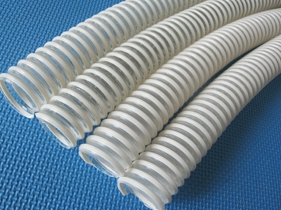
1. Mutual wear of rubber lining plate and steel ball of ball mill: both the rubber lining plate and steel ball of ball mill are vulnerable parts. During grinding, the steel ball and material of ball mill do throw line falling movement in the barrel Chongqing Oil resistant hose It will collide with steel balls and materials and cause friction. In continuous operation, the rubber lining plate and steel ball of ball mill will be severely worn, which is directly related to the hardness of materials. The greater the hardness of the material, the faster the abrasion speed of the rubber lining plate and steel ball of the ball mill, which may cause equipment damage or even safety accidents in serious cases. In addition, it is also related to the ball of the ball mill. The size and quantity of the ball will affect the service life of the rubber lining plate of the ball mill. If the ball mill is in operation, increasing the amount of steel balls or filling steel balls with larger diameters will increase the wear of the rubber lining plate of the ball mill. 2. The heat treatment process of the rubber lining plate of the ball mill is unreasonable: the unreasonable heat treatment of the rubber lining plate of the ball mill will not only increase the wear of the lining plate, but also affect the yield strength of the lining plate, resulting in the fracture of the bolt of the ball mill under the large shear force. In the actual operation, the staff lacked the understanding of the lining plate material and the heat treatment processing of the ball mill rubber lining plate was insufficient, so the strengthening effect of the ball mill rubber lining plate was not in place and the strength was low. When impacted by steel balls and materials, Oil resistant hose company Plastic deformation often occurs. 3. The material of the rubber lining plate of the ball mill is unreasonable: the material of the rubber lining plate of the ball mill and its heat treatment process are the key to determine the mechanical performance of the lining plate. If the material of the lining plate is not properly selected, its fatigue strength and life will be greatly reduced, which will not meet the requirements of the ball mill, or even plastic deformation or bulge will occur.
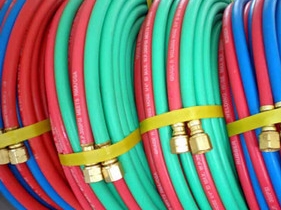
Prof. Weina, University of New South Wales, Australia? Sahajwara has developed a new method of using waste rubber and plastic for steel production - polymer injection process. Chongqing Oil resistant hose It can not only greatly reduce the environmental pollution caused by waste rubber and waste plastics, but also effectively reduce the cost of steel production. Waste rubber and plastic contain a lot of carbon. Waste rubber and plastic are put into the electric arc furnace as substitutes for carbon element. The carbon originally locked in the waste plastic hose will react at ultra-high temperature and burn with coal to become clean fuel, thus reducing greenhouse gas emissions, At the same time, it also alleviates the environmental pollution caused by using them as landfill. The advantage of polymer injection process is that by injecting polymer and coke or anthracite rubber tube mixture, the volume of slag can be increased and the foaming degree can be increased, which can extend the arc length, increase the heat transfer from the arc to steel, reduce the heat loss through the slag and side walls, and thus improve the power efficiency. This reduces power consumption by about 3%. For every 1 ton of steel, about 24% of the cost comes from the cost of electricity. After polymer injection technology is adopted, each furnace of steel is, Oil resistant hose company The average total amount of carbon injected can be reduced by 10%~20%. In addition, the potential price of polymer is lower than that of coke, and the total cost of carbon injection can be saved by 15%~35%.
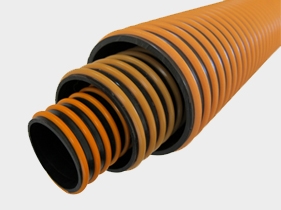
Chongqing Oil resistant hose Vulcanization of technical performance indicators is an important process to enhance the adhesive strength between rubber and reinforcement layer and make it a whole in rubber hose manufacturing, and also an important link to ensure and improve product quality. In order to obtain good pulse performance and service performance of steel wire reinforced rubber hose, in addition to reasonable structure and formula, it is necessary to ensure the compactness of vulcanized hose. In order to meet this performance requirement, the traditional vulcanization method is to wrap the water in water cloth on the semi-finished hose before vulcanization, make braided hose or steel wire for reinforcement and fastening, and vulcanize in batches with steam vulcanization tank. Since the performance requirements of medium and low pressure hoses are low, the rubber hose can also be directly put into the curing tank without fastening. Although water wrapped cloth vulcanization can also increase the compactness of the hose, its appearance is poor. In order to obtain the smooth outer surface of the hose, the lead coating vulcanization method is widely used at home and abroad. For decades, people have been using this method as an effective method to vulcanize and strengthen rubber hoses, especially high-pressure rubber hoses. So far, many domestic and foreign manufacturers are still using this method to produce rubber hoses. But the fatal disadvantage of this method is that it pollutes the environment. Oil resistant hose company The main control function of the air compressor station unit is to exhaust more air. According to different structures, it can be divided into full hose, cloth hose, steel braided hose, etc. According to different uses, it can be divided into air hose, water suction hose, water delivery hose, heat resistant hose, acid (alkali) resistant hose, oil resistant hose and special hose., It can be closed within the specified range.
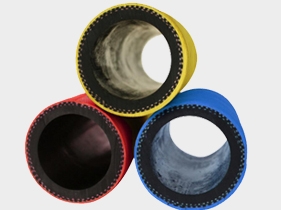
polyurethane high quality Oil resistant hose Maintenance measures; Cleaning: It is recommended to empty the hose after use. Clean if necessary. Inspection: After each use, the rubber tube must be inspected to ensure that there is no structural damage. Pressure: If the rubber pipe is under great pressure during use, or the outer layer of the rubber pipe will contact with the conveyed liquid for a long time, it is recommended to conduct a hydrostatic test. Due to the natural characteristics of rubber, the physical properties and performance levels of all rubber products will change. This change usually occurs over time, depending on the type of rubber used. However, changes may also accelerate due to several factors or a combination of several factors. Other materials used to reinforce rubber tubing may also be adversely affected by improper storage conditions. Detailed step 1. Polyurethane sand blasting pipe mandrel: the mandrel is usually pulled backward, mainly to increase the firmness of the connection between the mandrel and the hose. After the spindle barb processing is completed, the barb tip must also be passivated, otherwise the barb tip will pierce the lining material of the high-pressure rubber tube during the buckling process. Oil resistant hose company Even if the high-pressure rubber pipe joint is firmly buckled, if the inner layer is damaged, high-pressure water will leak from the buckle. 2. Polyurethane sand blasting pipe sheath: the sheath is generally in the form shown in the figure, the wall thickness should be moderate, and the internal rectangular tooth height should not exceed 2mm, that is, (d-d) should not exceed 4mm.
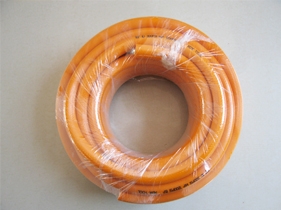
Chongqing Oil resistant hose The structure is composed of liquid resistant synthetic rubber inner rubber layer, medium rubber layer, I or II or III steel wire braid reinforcement layer, and weather resistant synthetic rubber outer rubber layer. Sand pumping hose features: 1. Sand pumping hose is made of special synthetic rubber, which has excellent oil resistance, heat resistance and aging resistance. 2. The rubber hose has high bearing pressure and excellent pulse performance. 3. The pipe body is tightly combined, soft to use, and has little deformation under pressure. 4. Sand pumping hose has excellent bending resistance and fatigue resistance. 5. The sand pumping hose is long, φ 20 meters above 32, φ Below 25 meters, it can reach 10 meters or even 100 meters. Sand pumping hose parameters: 1. The inner wall of nylon cord hose is smooth with little friction. Reinforcing layer: high-strength synthetic wire, spiral winding of steel wire and iron wire (sand suction pipe) 2 high quality Oil resistant hose Flange connection (ANSI150 standard flange) 3. Nominal pressure: 20BAR4, temperature: - 50 ℃ -+95 ℃ 5. Working pressure of sand suction hose and mud discharge pipe: positive pressure: 10kg; Test pressure: working negative pressure of 15kg steel ring sand suction hose: ≥ 15kg sand suction hose has strong flexibility, which is mainly used as the sand pump sand discharge pipe to connect the sand transport pipe and sand pump, as well as the pipe connection bend.