Current period Shandong sandblasting pipe manufacturer The matching system of oil resistant rubber is introduced in detail
1、 Oil resistant rubber
Oil resistance usually refers to the resistance to non-polar oils: fuel oil, mineral oil and synthetic lubricating oil.
Rubber is classified according to oil resistance (polar rubber): CR, NBR, HNBR, ACM, AEM, CSM, FKM, FMVQ, CO, PUR.
Classification of oil resistant rubber (non-polar rubber): NR, IR, BR, SBR, IIR, EPR, EPDM.
1 Fuel resistance:
Fluoroelastomer FKM and fluorosilicone rubber FMVQ have good resistance to fuel oil. However, neoprene rubber and chlorinated polyethylene rubber CPE have the worst fuel resistance. The fuel oil resistance of NBR increased with the increase of acrylonitrile content. Chlorohydrin rubber has better fuel resistance than nitrile rubber.
2 Mixed fuel resistance:
Fluorosilicone rubber FMVQ and Fluorosilicone FKM have good resistance to mixed fuel oil. Acrylate rubber has the worst resistance to mixed fuels. The mixed fuel resistance of NBR increased with the increase of acrylonitrile content. Fluorine rubber with high fluorine content has better stability for mixed fuel
Rubber gasoline/methanol 85/15 Average swelling degree (54 degrees)/% Gasoline/ethanol 85/15 Average swelling degree (54 degrees)/%
ECO 92 74
NBR 89 61
FMVQ2522
VITON A/FPM2601 23-28 16-20
VITON GH 19 15
BITON VI-R-4590 13 13
3 Acid resistance, oxidation and fuel oil resistance:
For acid oxidation fuel, the hydroperoxide in acid oxidation fuel can worsen the performance of vulcanizate, so the commonly used nitrile rubber and chlorohydrin rubber in fuel system cannot meet the requirements of long-term use. Only fluoroelastomers such as fluoroelastomer FKM, fluorosilicone rubber FMVQ, fluorophosphazene and hydrogenated nitrile rubber have better performance. The ordinary NBR compound cannot work for a long time in 125 ℃ acid gasoline. Only when the low sulfur sulfur donor activated by cadmium oxide and the NBR with white carbon black as the main raw material are used, can the acid resistant gasoline be better. Increasing the content of acrylonitrile can reduce the permeability of acid gasoline.
Mineral oil resistance:
NBR is a common mineral oil resistant rubber. The mineral oil resistance of NBR increased with the increase of acrylonitrile content.
However, the heat resistance of NBR with high acrylonitrile content is limited. When the oil temperature reaches 150 ℃, hydrogenated nitrile rubber, fluororubber FKM, fluorosilicone rubber FMVQ and acrylate rubber should be used.
When the oil temperature reaches 150 ℃, FKM and FMVQ of fluorosilicone rubber have good effect. However, the cost is high. In order to reduce the cost, less than 50% of acrylate rubber can be incorporated into FKM, and the performance of vulcanizate after use will decline by no more than 20%.
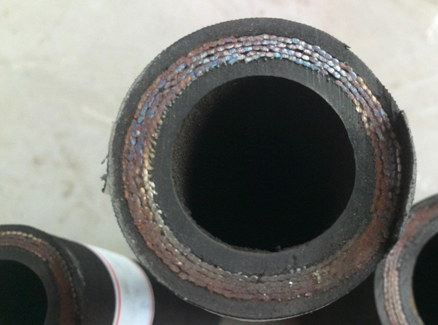
The mineral oil resistance of acrylate rubber is better than that of nitrile rubber. The heat oil resistance of ethyl acrylate rubber is better than that of butyl acrylate rubber.
4 Synthetic lubricant resistance:
The principle of similar compatibility: polar polymers are soluble in polar solvents, non-polar polymers are soluble in non-polar solvents, EPDM belongs to hydrogen rubber, which expands extremely in hydrogen oil, silicone rubber in silicone oil, and fluororubber in perfluorocarbon liquid.
5 Synthetic hydrogen resistant lubricating oil:
The oil resistance of NBR increased with the increase of acrylonitrile content. Aromatic hydrogens have greater swelling effect on NBR than aliphatic hydrogens. NBR with high acrylonitrile content is used for synthetic hydrogen oil with high aromatic hydrogen content. Acrylonitrile butadiene rubber with medium acrylonitrile content is used for synthetic hydrogen oil with low aromatic hydrogen content. NBR with low acrylonitrile content is used for synthetic oil such as paraffin oil used for low expansion. Or where low temperature flexibility is more important than oil resistance. The use of hydrogenated acrylonitrile butadiene rubber can improve the heat resistance, ozone resistance and resistance to additives. Hydrogenated acrylonitrile butadiene rubber is suitable for the occasions with 140-150 ℃ hot oil resistance. Oil resistance and heat resistance are between NBR and fluororubber. Fluoroelastomer can withstand 200 ℃ synthetic hydrogen lubricating oil for long-term operation. Silicone rubber can withstand 200 ℃ synthetic hydrogen lubricating oil for long-term operation. And maintain good flexibility at - 60 degrees. It is good for paraffin oil and PAOS. But it is not resistant to synthetic hydrogen oil with low viscosity. It will cause great expansion. Chlorohydrin rubber can work for a long time in synthetic hydrogen lubricating oil at - 40 to+120 degrees, with low permeability and good ozone resistance. The defect is the corrosion to the mold and the returning phenomenon after high temperature aging. The resistance of chlorosulfonated polyethylene rubber to synthetic hydrogen lubricating oil increases with the increase of chlorine content. In the range of - 20 to+120 degrees, it can only be used in high paraffin mineral oil PAOS, and it expands greatly in naphthenic oil and aromatic hydrogen oil. Polyurethane rubber AU/EU/is also resistant to synthetic hydrogen lubricating oil, but its compression deformation tends to deteriorate with the increase of temperature (over 70 ℃). In addition, the hydrolysis resistance is poor.
6 Synthetic lubricating oil resistant to polyalkylene glycol (PAG)
Generally, acrylonitrile butadiene rubber, neoprene rubber, EPDM vulcanizate with proper formula can resist PAG synthetic lubricant. But neoprene and EPDM are not resistant to mineral oil. A little mineral oil in the system may cause extreme expansion. Fluoroelastomer is not resistant to PAG synthetic lubricant. Organic ester resistant synthetic lubricants are divided into two categories: dicarboxylate and polyol esters. Generally, suitable combination of NBR and fluororubber phosphate resistant synthetic lubricating oil is selected. Silicone rubber can resist phosphate ester synthetic lubricant, but its physical properties are very poor, and its use is limited. EPDM and butyl rubber can only resist pure phosphate ester. If a small amount of mineral oil is mixed, it will expand. Fluoroelastomer is not resistant to phosphate ester synthetic lubricant. Ethylene propylene diene monomer rubber, ethylene propylene diene monomer rubber and butyl rubber can work for a long time in phosphate ester synthetic lubricating oil below 121 ℃
Resistant to synthetic lubricants containing silicon.
Generally, silicone oil is not easy to cause rubber expansion, but it can pull out the plasticized part of the rubber. Styrene butadiene rubber, EPDM rubber, acrylonitrile butadiene rubber, hydrogenated acrylonitrile butadiene rubber and fluororubber that are not plasticized are resistant to silicone liquid
7 Fluorine resistant oil
Poly (perfluorohydroxy ether) is a non combustible liquid, which can be used in the temperature range of 230-260. None of the known rubbers can work in this temperature range for a long time. EPDM can be used in 100 ℃ fluorine containing oil. Viton can be used at 150 ℃.
8 Polyphenylene ether resistant liquid
Polyphenylene ether is the most radiation resistant liquid and is extremely stable to high temperature and oxidation. EPDM can be used in 100 degree polyphenyl ether. Viton can be used at 200 ℃. But fluororubber is not resistant to radiation.
9 Chlorinated hydrogen resistant liquid
The synthetic liquid of hydrogen chloride is a non water based flame retardant liquid. Fluoroelastomer and silicone rubber have good effects.
2、 Matching system of oil resistant rubber
1. Vulcanization system
In general, increasing the crosslinking density can improve the oil resistance of vulcanizates. In oxidized fuel oil, NBR vulcanized with peroxide or semi effective vulcanization system has better oil resistance than sulfur vulcanization. The NBR vulcanized by peroxide curing system has good stability at 40 ℃, but is not ideal at 125 ℃. However, NBR vulcanized with cadmium oxide and sulfur donor system has better long-term heat aging resistance in 125 ℃ oxidation fuel.
2. Filling system and plasticizer
Oil resistance can be improved by adding carbon black and white carbon black. The softener that is not easily extracted by oil should be selected. Select low molecular polymer, such as low molecular polyethylene, oxidized polyethylene, polyester plasticizer and liquid rubber. Softener or plasticizer with large polarity and molecular weight is favorable for oil resistance.
The above is Shandong Sandblasting pipe About the arrangement of the manufacturer Oil resistant rubber matching system.