1. Rubber hose
Sand blasting hose manufacturer The hydraulic hose is composed of an inner rubber layer, a reinforcing layer and an outer rubber layer. The inner rubber layer is in direct contact with the oil, so it should not be corroded by the fluid under long-term working conditions and can prevent leakage. It can bear certain pressure under the action of reinforcement layer. Sandblasting hose The manufacturer said that besides the rubber compound, the main factors affecting the performance are the hardness, thickness and deformation of the inner rubber layer. High hardness, small deformation after compression, and better sealing performance. Generally, it is better when the hardness is 70-85 Shore and the compression deformation is 50%. The thickness of the inner rubber layer is 1.5-2.5mm. If it is too thick, its flow rate will increase during buckling, resulting in the accumulation of excess rubber in the contact end face between the joint core sleeve and the rubber tube, reducing the flow section; Too thin will be fractured during buckling. At the same time, the wall thickness uniformity of the inner glue layer is also very important. If the thickness is uneven, one side will break and the other side will pile glue after compression. Pits on the surface of the inner glue layer are also important factors affecting the performance and quality.
The hydraulic hose mainly relies on the reinforcement layer to bear the pressure. The braided hose is fastened by the glue and the inner and outer glue layers. Due to the mutual contact between the steel wires in the same braid, the friction between the steel wires will affect their durability due to their different expansion and contraction under dynamic pressure. The winding pipe is a working layer formed by two layers with different winding directions, and there is intermediate glue between the two layers, so there is no intersection between two layers of steel wire in the same working layer. Therefore, it will not form stress concentration or friction and wear due to cross bending between steel wires under dynamic pressure. Therefore, it has good durability and can withstand high pressure.
The outer rubber layer of the hydraulic hose is attached to the reinforcement layer for protection, and neoprene is generally used. Attention shall be paid to prevent aging and cracking which may affect the service life of the entire hose
2. Connector
The buckle type rubber hose joint is composed of a joint core, a nut and a jacket.
1) The main factors affecting the performance of joint core are the length of core rod, structural shape, wall thickness and material. From the perspective of sealing and prevention of pulling out, the longer the core rod, the better, but too long will waste materials and increase manufacturing costs. In addition, in order to prevent glue stacking at the end of the core during pressing, the length of the core is generally required to be slightly longer than that of the jacket.
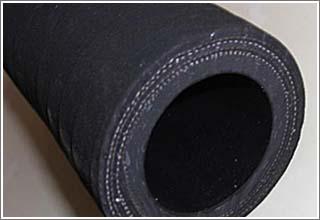
2) There are many configurations of the core rod, among which R groove and zigzag groove can increase the friction surface and provide rubber holding groove for rubber flow.
3) Material: The joint core is generally made of 20 #, 35 # and 45 # carbon structural steel. In order to prevent the deformation of the inner hole of the core during buckling and increase the liquid resistance, the core wall thickness is generally 1.5-3.5 mm. The larger the drift diameter is, the larger the interference between the outer circle of the core and the inner hole of the rubber tube is, the inner rubber will be damaged, making it difficult to fit the cavity. If the inner hole of the core is too small, it will increase the liquid resistance and cause pressure drop loss. The outer diameter of the core is subject to the above restrictions. The size of the hose itself varies greatly. In order to meet the requirements of the lower limit of the performance throughput of the joint assembly, it must be solved by optimizing the amount of buckling.
3. Connector jacket
The size of its inner hole should be appropriately larger than the size of the reinforcement layer, otherwise it can not be installed, or even the reinforcement layer will be completely scattered. The general clearance is 1-1.5mm. The groove shape inside the jacket will directly affect the joint quality. At present, there are straight hole slotless type, serrated groove type and annular and serrated groove combination type.
Cotton thread (fiber) Braided hose Because of low use pressure and small pull-out force, all adopt slotless structure. The reinforcing layer of the steel wire braided hose is prone to bending deformation when it is buckled, and most of them are zigzag. Generally, the steel wire wound pipe has many layers, and the thickness of one side of the reinforcement layer can reach 3.6 mm. To make the reinforcement layer form wavy deformation and embed into the groove during buckling, the combination of circular and serrated grooves must be used. This groove is 2/3 wider than the serrated groove, and its anti pulling force is stronger.