Sandblasting hose The mesh sleeve of is made of metal wire and wire, which is the external protective layer of sandblasting hose. Its damage sample mainly includes the damage of metal ribbon, broken wire, and bulge of mesh sleeve. Generally, overloading the use of sandblasting hose will cause damage to the mesh sleeve. In the use of sandblasting hose, if the acceptance limit of the metal mesh sleeve is exceeded, the mesh sleeve will produce an obvious bulge scene.
1. Mesh sleeve is too loose
When the sandblasting hose is on duty, the transverse load in the internal downforce caused by the medium is borne by the bellows, and the outer net sleeve receives the longitudinal load. As most nets are woven by machines, when the nets are too loose and cannot bear the side pressure of the longitudinal load, the nets will bulge from time to time.
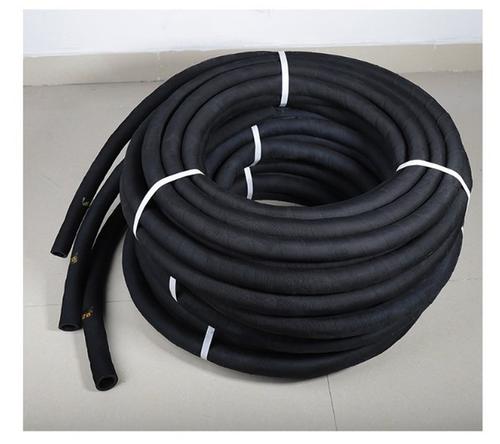
2. The braiding angle is too large
If the braiding angle of the sandblasting hose is too large during the braiding process, the coverage rate of the mesh sleeve will be too large, the mesh sleeve will be loose, and the mesh sleeve and the corrugated pipe will not fit closely. When the corrugated pipe is deformed, it is easy to produce bulges.
3. The bending radius is too small
In the process of installation, because the installation of sandblasting hose is limited in half space Sandblasting hose For example, the nominal size is DN150, the rigid section length of the test piece is 100 mm, the longitudinal offset is 250 mm, and the installation of small bending radius is 1800 mm. It is reasonable to measure that the length of the small test piece is 7 525 mm, but the actual length is 10 000 mm. Due to the limited space, the hose will bend for some spans, Subsequently, the outer pressure bearing prefabricated member net sleeve deforms, and bulges appear.
Note: The above content comes from the network. If there is infringement, please contact the administrator to delete it. Thank you.