(3) Steam pressure forming
Common on construction site Sandblasting pipe Quality problems and solutions
(a) Inner cavity surface F+P (b) Surface surface F+P
The alloy composition of the inner and outer wall surface layer of the tee, for the tees with large diameter and thick wall thickness, the rear two forming methods are mostly selected, and the forming time of these two methods generally must be 1~2 minutes, even up to 3 minutes. In this few minutes, how to maintain the relative stability of temperature is a crucial issue for the quality of the sandblasting pipe. If the temperature difference is too large, it will lead to the imbalance of the fluidity of the concrete fiber mechanism, especially in the location where the deformation is very large. It will cause a large plastic deformation. If the temperature is too low, it will lead to the cold hardening condition and cause ductile damage.
From the alloy composition, the tee pipe has a remarkable strip mechanism, and the strip mechanism at the fracture El (transverse) is more remarkable than that at all normal positions, which indicates that the position has undergone a great plastic deformation and low magnification inspection at the fracture surface (transverse), the external appearance of the ferrite is normal, and the cementite agglomeration and spheroidization are not observed, This shows that the temperature of tee in extrusion molding is low.
The strip mechanism at the shallow surface layer (about 0.4~0.7 ram) of the tee is not significant, while the strip mechanism in the inner cavity is very prominent. This shows that the temperature difference on the surface of the tee is large, the temperature is high and the cooling rate is fast. It can be seen from the macro diagram of three-way products that there are defects (crack sources) near the position where the strain force is large (i.e. the root of the three-way) during the three-way extrusion molding. After molding, the length of cracks on the inner surface layer is up to 40 ram. All cracks are listed.
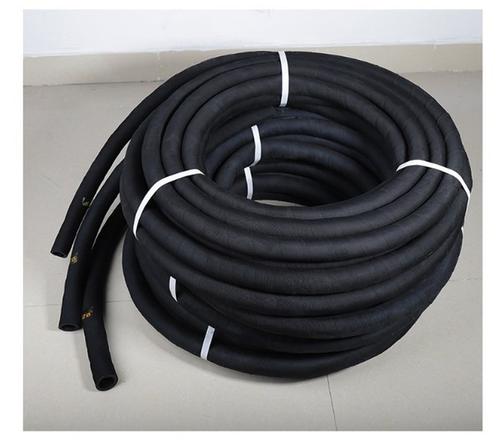
The surface is covered by thick oxide skin. From the color of the surface (light yellow, red purple, blue gray, dark brown, etc.), it should be Fe3O.
(a) Surface crack shape (b) Inner cavity crack appearance
From the panoramic view of fracture El (Fig. 5 and Fig. 6), it can be seen that fracture H is covered by oxide skin, which is about 45mm long and basically surrounds the wall thickness, and the color of the metal oxides around the crack layer is basically the same as that of the metal oxides on the inner surface of the wall thickness, indicating that the metal oxides on the crack source and the inner surface of the cavity are produced under the same standard. In addition, the metal oxide is fused and tightened with the conventional method, which is difficult to remove even after cleaning with hydrochloric acid solution. The inner edge of the metal oxide on the fracture surface is connected with the metal oxide on the inner surface, which indicates that the metal oxide is produced under the same natural environment.
Many test results above confirm that the stress at the surface defect (crack source) of the tee caused by the defects of the manufacturing process during hot extrusion molding makes the crack expand until it is close to the surrounding and the crack fracture El is smooth, with the characteristics of transient fracture El. The crack development direction is consistent with the deformation trace during extrusion molding of the tee. All these indicate that the cracks are generated in the whole process of i-way extrusion
3.3 Heat treatment process after forming
The final heat treatment process after tee forming can significantly improve the physical properties of steel. Especially for tee production plants with production and processing methods, it is critical to select appropriate heat treatment process rules and regulations and processing technology. In GB12459-90 "Steel butt welded seamless pipe fittings", it is required that r cold formed galvanized steel pipe fittings shall be subject to quenching or quenching heat treatment process. So which heat treatment process should be selected, especially which quenching rules and regulations should be selected, is not selected or indicated in the specification, which depends on the production, manufacturing and processing process. Xiao Bian believes that no matter which kind of heat treatment process rules and regulations are selected, the purpose is to improve the physical properties and compressive strength of the sandblasting pipe. During the whole process of hot forging of sandblasting pipe, the steel structure will cause great transformation due to its great plastic deformation, such as; The strip mechanism is remarkable, the crystal is thick, dislocation displacement, page load and so on. This kind of mechanism transformation is very harmful to the drilling production and performance index of steel. In order to get rid of this bad transformation, the transformed organizational structure should be changed according to the heat treatment process, so that its crystal is optimized and its mechanism is symmetrical. To achieve this goal, it is necessary to use quenching or the thorough quenching process in quenching. Many sandblasting pipe manufacturers have not yet fully understood this point. Due to some kind of consideration, they only carried out quenching heat treatment process dedicated to removing in-situ stress for formed sandblasting pipes, and this kind of quenching has not yet changed the alloy composition and characteristics of sandblasting pipes from the source, which cannot ensure the quality of sandblasting pipes.
four Sandblasting pipe Pre factory and post delivery inspection
As the final process flow to ensure the quality of the sandblasting pipe, the detection plays a key role, especially for the sandblasting pipe bearing ultra-high pressure and flammable toxic substances, the whole process of detection is crucial. At the present stage, the sandblasting pipes are mostly inspected for appearance, strength, thickness, magnetic particle flaw detection (MT) and ultrasonic flaw detector (uT) before the original factory. From the inspection of the sandblasting pipes delivered, the most difficult problems are the magnetic particle flaw detection and ultrasonic flaw detector. For magnetic particle inspection, the manufacturer usually applies the yoke method (galvanized steel pipe). However, due to the limitation of machinery and equipment, most of these methods are limited to the outer surface of the sandblasting pipe, and the most difficult problem is just in the inner cavity of the sandblasting pipe. For the cracks that usually occur in this part, especially the cracks in the inner cavity of the small-diameter sandblasting pipe, Magnetic rod method or vortex method should be used to carry out ultrasonic flaw detector detection, which is a new detection project with high regulations on machinery, equipment and technology, because:
1) It stipulates that the operator should have high technicality and rich and colorful work experience, and whether the detected defects belong to cracks or others should be given