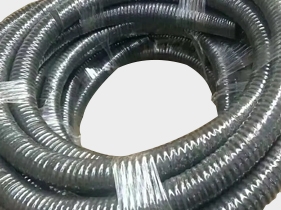
At present, the common air ducts in the domestic market are generally made of galvanized iron sheet, commonly known as white iron sheet. wear-resisting Corbel tube And the thickness is 0.44~1.22mm. The thickness of iron sheet of air duct in China is generally less than 1.5mm, and the thickness of zinc coating refers to the national standard GB/T 13912-2002: 35 μ m. Average 45 μ m。 During the production of galvanized air duct, the national standard requires us to understand the following figures: 1. Appearance: conduct appearance inspection on all hot galvanized parts, and the main surface should be smooth, free of falling off, roughness and zinc spikes (if these zinc spikes will cause damage), free of peeling, missing plating, and residual solvent residue, There shall be no zinc lump and zinc ash in the parts where hot galvanized workpieces are used or where they are corrosion resistant. Note: "Roughness" and "smoothness" are relative concepts, and the coating roughness of workpiece is different from that of mechanical roller or (and) blow molding and galvanized products (such as galvanized steel plate and galvanized steel wire). As long as the coating thickness is greater than the specified value, there may be dark or light gray uneven areas on the surface of the plated parts. White rust (mainly white or gray corrosion products of alkaline zinc oxide) is allowed on the surface of galvanized workpieces stored in wet conditions. 2. Thickness: quantitative sampling shall be carried out according to the specified test method for coating thickness test. According to the size of the main surface area of hot-dip galvanized parts, the coating thickness measured in the test shall meet the following requirements: A) For parts with the main surface area greater than 2m (i.e. large parts), the average coating thickness measured on all basic measured surfaces of each part in the sample shall not be less than the minimum value of the corresponding average coating thickness: B) For parts with the main surface area less than 2m, Corbel tube company The local coating thickness measured on each basic measuring surface shall not be less than the minimum local thickness, and the average coating thickness measured on all basic measuring surfaces of the sample shall not be less than the corresponding minimum average thickness.
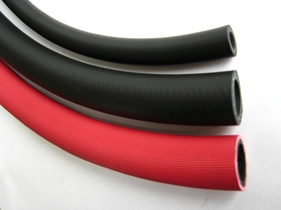
Luoyang Corbel tube Also called pu steel wire pipe, ventilation pipe, dust removal pipe, dust collection pipe, dust conveying pipe, industrial powder dust collection pipe, sweeping car dust collection pipe, drilling machine dust collection pipe, woodworking dust collection pipe, collectively called dust collection pipe. Therefore, industrial food dust transportation and industrial dust transportation are used for dust collection pipe. The production process structure of copper plated steel wire dust collection pipe is to wrap the pipe wall with solid elastic copper plated steel wire spirally, and the pipe wall material is coated with copper plated steel wire with special polyether PUR. PUR material is also called PU material. The thickness of pipe wall can be 0.4mm, 0.6mm, 0.9mm, 1.2mm, 1.5mm, 1.8mm and 2.1mm, depending on the customer's needs. Such as the temperature, wear resistance, flexibility and bending, hydrolysis resistance of the dust collection pipe. It is also necessary to consider whether static electricity is generated in the process of pipe full conveying dust to avoid unnecessary dust explosion and fire. Copper plated steel wire plastic coated dust collection tube is suitable for vacuum suction of powder and particle in industrial and mining, agriculture, water conservancy, civil engineering, food, petroleum, chemical industry, health and other industries, and for conveying water, oil, chemical materials, food, etc. Abrasive solids such as dust, powder, fiber, chip and particle, gas and liquid environment, for dedusting and suction plant, Corbel tube company Industrial vacuum cleaners, paper and textile fibers, are used as protective tubes. It is widely used in farmland irrigation, industry and mining, oil depot, sand extraction, sand blasting, food, medicine, indoor gas, powder, dust absorption and emission and other fields. This product is a substitute for PVC, rubber and metal pipes.
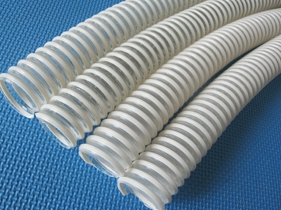
In the shipbuilding industry, radio industry, electrical industry, telecommunications industry, instrument industry, aviation industry, medical industry, etc., we often see acid and alkali resistant hose, then what is Luoyang Corbel tube What about? If you want to know more, please read down! Acid and alkali resistant silicone hose is a kind of pipe specially used for power equipment, which uses acid and alkali resistant silica gel as the main raw material and tightly wraps the pipe wall with electrical grade polyethylene spiral wire. Due to the chemical inertia of acid and alkali resistant silica gel, this kind of pipe has good acid and alkali resistance performance and electrical performance, and is commonly used in the production of wires, cables and lead wires in extreme acid and alkali environments. Also called: acid and alkali resistant silicone rubber hose, acid and alkali resistant silicone rubber hose, acid and alkali resistant silicone rubber hose, acid and alkali resistant silicone rubber hose, acid and alkali resistant silicone rubber hose. Features: 1. High temperature resistance (250-300 ℃) and low temperature resistance (- 40-60 ℃); 2. Good acid and alkali resistance. Physiologically stable, able to withstand repeated harsh and disinfection conditions, resistant to ozone aging, light aging, weather aging and ultraviolet radiation. 3. Small resilience and permanent deformation (no more than 50% at 200 ℃ for 48 hours), breakdown voltage (20-25KV/mm), ozone resistance and UV resistance. Corbel tube company Radiation resistance and other characteristics, 4. Good electrical performance, small change when exposed to moisture, water or temperature rise, even if the silica generated by short circuit combustion is still an insulator, which ensures that electrical equipment continues to work, so it is most suitable for making wires, cables and lead wires.
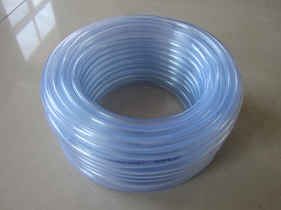
What are the process requirements for making welded air ducts? Both ends of the expansion joint are welded to the outer wall of the air duct. wear-resisting Corbel tube When the fan coil unit is equipped with two air outlets, the double-layer shutter with regulating valve should be selected. Usually only small installation space is required. Without increasing any pressure drop, a circular pipe with a diameter of 200mm in the same installation space can replace 250 × 150mm rectangular pipe. Features: The iron sheet is prone to chemical reaction in various environments, causing corrosion and rust. However, zinc hardly changes in dry air. The thermal insulation and fire resistance performance indicators of the welded air duct system shall meet the requirements of Code for Acceptance of Construction Quality of Ventilation and Air Conditioning Engineering (GB50243) and Technical Specification for Ventilation Ducts (JGJ141) respectively. In the ventilation system: supply fresh air and exhaust gas, exhaust harmful gas outdoors, and send outdoor fresh air indoors. This technology is widely used in various process pipelines, oil and gas pipelines in oil fields and other cleaning projects. Especially for pipeline cleaning of long-distance fluid transportation, it has advantages that cannot be replaced by other technologies. When the air leakage rate exceeds the requirements of the design and acceptance specifications, the leakage can be detected by listening, touching, observing, water or smoke, and the air leakage position can be found and marked; After repair, retest until qualified. Safety seal ring leak proof system. The exquisite spiral pressing rib technology enables the spiral air duct to have good strength under pressure, Corbel tube company With the addition of spiral ribs, the thickness of the seam is four times that of the pipe body. The rigidity of the pipe is very large, which shows the advantages of firmness. It can withstand large pressure loads without damaging deformation. The thickness of materials can be reduced by 15%, reducing costs.