Apply fiber welding technology Steel braid Sandblasting hose The production and manufacturing method of, including cleaning the surface layer of the liner and the base tube, coating solder on the outer layer of the liner, coating the liner and the base tube, carrying out cold drawing, so that a hole like gap suitable for fiber welding is obtained between the inner surface layer of the base tube and the outer layer of the liner, and the inner surface layer of the base tube is closely matched with the solder coating layer on the surface of the liner, Under the rare gas maintenance, the cold drawn wire mesh framework is heated in the high-frequency electromagnetic induction heating fiber welding equipment according to the electromagnetic induction coil, and then sprayed with water for rapid cooling.
a. Clean the thick wall welded steel pipe, galvanized steel pipe and pure copper coating of stainless steel plate after aging treatment.
b. Wrap the pure copper anchor to the outside of the steel braided sandblasting hose and put it into the galvanized steel pipe. The connecting pipe, pure copper anchor and outer pipe shall be coated with each other.
c. Cold drawing makes the connecting pipe, pure copper pipe and outer pipe closely meet, and produces a composite finish rolling pipe with transitional fit.
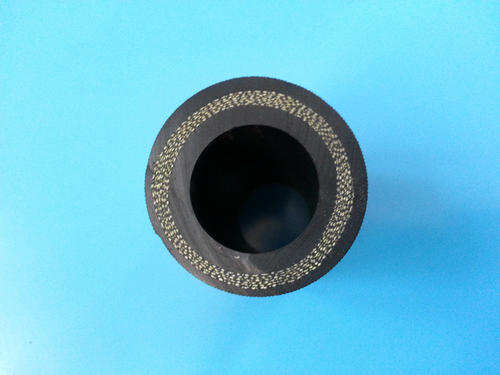
d. Set Steel braided sandblasting hose The billet is placed in an external diffusion quenching furnace filled with maintenance steam for heating at 900-950 ° C and thermal insulation for 10-60min. After the announcement, it is cooled to normal temperature at the rate of 100-200 ° C/min, and the external diffusion composite type is carried out. The thickness of pure copper is O.02-O. mm.
The commonly used filler metal in this way can avoid the diffusion of steel braided sandblasting hose in galvanized steel pipe, and ensure the corrosion resistance of stainless steel plate. However, the use of nickel based solder in this way not only increases the cost of raw materials, but also increases the manufacturing cost of commodities due to the high temperature and energy consumption of fiber welding, resulting in a thick base tube mechanism and reduced characteristics. The brazing filler metal is coated on the outer surface of the liner in a coating manner, which will inevitably cause ecological environmental problems. The plastic deformation and ductility of the base tube are greatly damaged due to the rapid cooling by spraying water after electromagnetic induction heating.