Sandblasting hose The amount of joint compression directly affects the joint connection performance. High pressure rubber hose is composed of steel wire reinforcement layer and inner and outer rubber layer, which is orthotropic. In this paper, the rubber hose is regarded as an anisotropic cylindrical shell by using the rubber composite theory, and the buckle pressure is considered.
Rubber hose connection is the most common cold connection technology. There are two types of connection between connector and hose: buckle type and detachable type. The buckle type hose joint is simple in structure, reliable in use, small in size and convenient in processing. The buckle press is used for buckle pressing. The compression amount of the compression type hose joint directly affects the joint connection performance. The buckle type rubber hose assembly is a fixed pipe joint structure that cannot be disassembled. This structure can form a great clamping force between the rubber layer and the joint. The sealing of the joint is completed by the inner rubber layer of the rubber hose deforming the inner rubber layer with the help of the outer sleeve and the core. The connection strength is ensured by directly pressing the outer sleeve to make the rubber hose get a certain amount of compression, so as to fasten the steel wire of the braided layer (or winding layer).
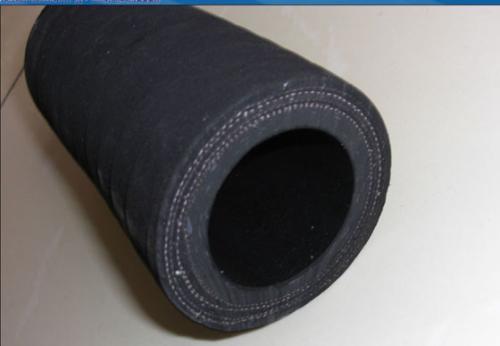
High pressure rubber hose is composed of three main parts: inner rubber layer, reinforcement layer and outer rubber layer. These three parts have an important impact on the service performance and life of rubber hose. They ensure the strength, sealing and stability of high pressure rubber hose. The inner rubber layer is located at the innermost layer of the rubber hose, ensuring the sealing of the high-pressure rubber hose, and protecting the bearing reinforcement layer (steel wire) from the turbidity of the working fluid. The reinforcing layer is composed of several layers of steel wire braiding (or winding), which is located between the inner and outer rubber layers to ensure the strength stability and good tensile property of the high-pressure rubber hose; The outer rubber layer protects the high-pressure hose from external factors.
The first batch of Steel wire braided rubber hydraulic hose It was produced by the American Rubber Company in 1938 and the British Dunlop Company in 1939. In the late 1970s, steel wire braided and wound reinforced hoses were produced by a few domestic manufacturers and began to be put into the market [1]. However, for its buckling process, generally only the mechanical analysis is conducted for the sleeve modeling, and there has not been a relatively complete mechanical model to describe it. In this paper, the general mechanical model is obtained through theoretical derivation, and the whole rubber hose joint buckling process is simulated and calculated through ANSYS finite element simulation and experimental demonstration. Therefore, it is beneficial to determine the reasonable amount of buckling and improve the comprehensive performance of the hose joint.