Wear resistant hose Used for mine hydraulic support, oilfield development, engineering construction, lifting and transportation, metallurgical forging, mining equipment, ships, injection molding machinery, agricultural machinery, various machine tools and mechanization of various industrial departments The automatic hydraulic system is used to transport petroleum based liquids (such as mineral oil, soluble oil, hydraulic oil, fuel oil, lubricating oil) and water-based liquids (such as emulsion, oil-water emulsion, water) with a certain pressure and temperature and liquid transmission pipelines.
Improper use
On the premise that the quality is guaranteed, if the hose is used improperly, the service life of the hose will be greatly shortened. In practice, most of the wear resistant hose ground damages are caused by improper use.
Be subjected to repeated and severe pressure shock. The burst of wear-resistant hose is generally not caused by too much static pressure, but is related to the intensity and number of pressure shocks.
During the operation of construction machinery, the sudden rise or fall of oil pressure in the oil pipe will occur repeatedly, which will then constitute repeated pressure shocks to the oil pipe, leading to the aggravation of oil seal damage in each part, blistering and splitting of rubber hose, and loosening and leakage of pipe joints. Therefore, during operation, the valve rod shall not be pulled too hard, and must be steep.
The operating temperature of the oil is too high. During the operation of construction machinery, the hydraulic system heats the oil due to power loss, and the influence of external temperature (especially in summer) can make the oil temperature rise sharply. The higher the operating temperature of the oil, the easier the banana is to age, the worse the elasticity, the lower the strength and sealing function, and the hose will burst quickly.
During operation, if the temperature rise of the hydraulic system is too high or too fast, find out the cause in time and clean it; Necessary cooling measures shall be taken for operations in summer, especially continuous operations.
The selection and installation of rubber hose are unreasonable. When replacing the wear-resistant hose, the length, steel wire layers, joint shape and size of the selected hose should be reasonable, and the bending degree of the hose should be minimized
When tightening the joint nut, do not distort the hose. Excessive bending and distortion will greatly reduce the service life of the hose; Protective measures shall be taken for some parts with simple conflicts to prevent the hose from bursting due to wear.
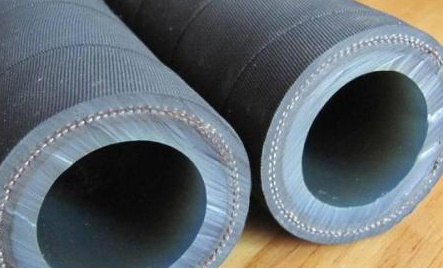
Poor manufacturing quality
The inner and outer layers of the wear-resistant rubber pipe wall are oil resistant rubber, and the middle layer (2~4 layers) is interspersed with braided steel wire or surrounding steel wire. Poor quality hose will appear: uneven thickness of hose wall; The steel wire braiding is too tight, too loose or the number of steel wire layers is too small; The deformation (elongation, shortening or bending deformation) of the hose after pressurization is large; Steel wire corrosion due to poor air tightness of outer glue
The poor sealing of the inner layer glue makes the high-pressure oil easily enter the steel wire layer; The adhesive force between adhesive layer and steel wire layer is insufficient. All of the above conditions will reduce the bearing force of the hose, and eventually burst at the thin part of the pipe wall.
Improper selection of the amount and speed of buckling for the hose and joint device, or improper selection of the structure, material and dimension of the joint, may lead to the over tightening or loosening of the pressure between the hose and the joint, which may result in early damage at the joint.
When installing, if the amount of crimping is too small, that is, the pressure between the joint and the hose is too loose, the hose may come out of the joint at the initial stage of use under the effect of oil pressure
If the amount of buckling is too large, the joint and the rubber hose are pressed too tightly, which is likely to cause local damage to the inner layer of the rubber hose and crack. High pressure oil will enter the steel wire layer directly from the split point, and then flow along the gap between the steel wires to the tail of the outer jacket, or flow along the steel wire layer to a certain place to accumulate, causing the outer layer of rubber to bulge or even split.
When the rubber hose and joint are installed, if the buckling speed is too fast, the internal rubber damage and steel wire layer crack will be simply formed, which will cause premature failure of the rubber hose in use.
Unreasonable joint planning and poor processing quality will also result in Wear resistant hose Damage; If the joint material is improperly selected, it is easy to deform during the buckling process, which will affect the buckling quality and shorten the life of the hose.